3D Printing in Engineering is Finally Living Up to the Hype
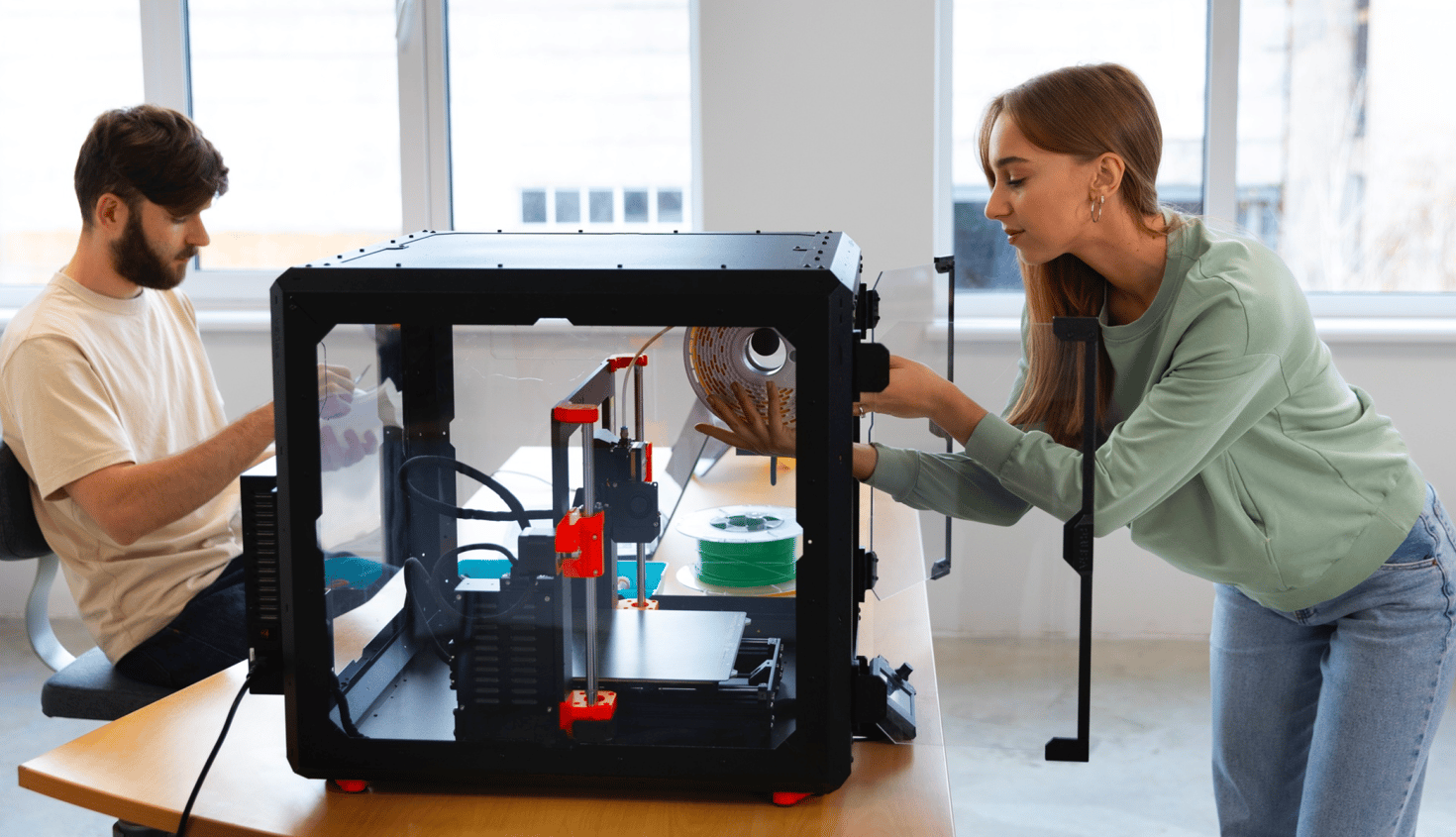
3D printing worked its way out of laboratories through eager adopters and, finally, to big engineering. Accurate educational models, hundreds of small but complex parts in a matter of hours, affordable artificial limbs – these are just a few of its applications. Engineering is one of the industries that has learned to use the benefits of 3D printers to the fullest. Let’s take a look at how 3D printing is applied in various fields of engineering.
Top 3D Printing Trends in Engineering
Engineering gradually moves from 3D-printing prototypes to fully functional parts. Kirk Rogers from the GE Center for Additive Technology divides additive manufacturing (AM) into the following groups:
- level 0: Jigs and Fixtures
- level 1: Components
- level 2: Subsystems
- level 3: Functional Integration
- level 4: Advanced Functionalities
At the moment, companies 3D-print elements from level 0 to level 3, while level 4 is mostly tested in research institutions. To have a better understanding of this year’s tendencies and innovations of 3D printing in engineering, we’ll focus on different spheres of its application.
Wholesale Automation
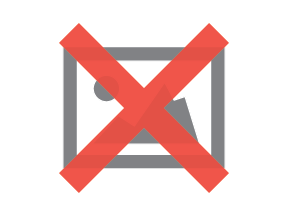
Manufacturing and wholesale are the industries that can take full advantage of 3D, as opposed to the individual use of personal 3D printers. It is an innovative and advanced type of automation that’s moving from prototyping to manufacturing ready-to-use functional products.
According to Statista, between 2017 and 2030, the global additive manufacturing market will shift from prototyping to mass producing parts and accessories. It also forecasts that by 2030, additive manufacturing technologies will allow companies to produce finished products on a large scale.
The traditional manufacturing process involves creating separate details and then assembling them into the working model. 3D printing allows eliminating the assembly phase from the production process, making the whole production far more efficient. Printers create the entire product at once, including all moveable elements that would be traditionally manufactured separately.
3D printing also significantly reduces or even entirely excludes lead time between the stages of design and production. Here’s the traditional workflow: design – prototype creation – prototype testing – revisions and improvements – actual production. 3D printing goes from design straight to production and lets you skip everything in between.
Experts claim that more industries in more countries will commercially apply 3D printing in the near future. Automotive, aerospace, heavy manufacturing and medicine will be among the trailblazers.
Metal 3D Printing
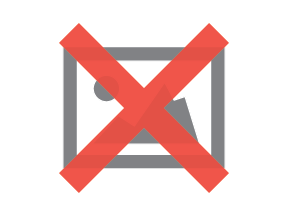
The branch is developing rapidly as a complementary technology. It will never replace traditional metal manufacturing, says Bart Van der Schueren, CTO at Materialise, but it becomes a necessity for big producers to lower the costs and stay commercially viable.
To meet the demand, the 3D Systems company is expanding its printing line with larger and more automated systems. They also promise to add a wider range of metals for direct printing in 2018. Another 3D printing supplier, Markforged, is releasing the new Metal 3D X Printer that is ten times cheaper and easier to use than the current models of metal printers.
The Oak Ridge National Laboratory (ORNL) is busy improving their existing metal 3D printing systems. It has revealed that the 2018 year research will help to increase process scale and deposition rates by enhancing the qualification and certification for AM metal parts. Also, ORNL is examining new light-weight and high-temperature metals to improve energy efficiency.
Although metal 3D printing is surrounded by hype at the moment, Scott Reese, senior VP at Autodesk says that 2018 won’t be the year that additive manufacturing becomes a fully functioning adult fending entirely for itself. Mr. Reese adds that there will still be considerable growing pains as AM matures.
Mass Customization
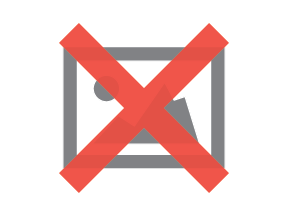
The survey of 1 000 Amazon shoppers showed that 25% to 30% are interested in using customization options. Adding customization options results in more loyal, regular and generous customers. And while customizing, say, clothes or footwear is not a big deal, it doesn’t work the same way with more complex products. This is where 3D printing steps in.
Mass customization (sounds quite oxymoronic, doesn’t it?) means smaller production sizes with low unit costs. Traditionally, to make any changes to the initial model (customize it), the entire work process has to be modified to manufacture a slightly different unit. With 3D printing, you simply upload a new digital file, without the need to change tools and molds.
This saves time and money tremendously. 3D printing is great for customizing various things, from insoles to dental prosthetic crowns and hearing aids, to custom automotive parts and more.
Production of Small, Complex, Expensive Products
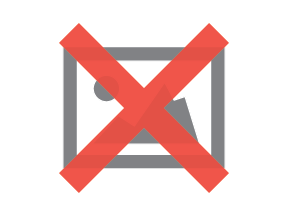
Once again, we are talking about big bucks saved with the help of 3D printing during the manufacturing process. A well-known example of using AM to create a ready-to-use product is the design of the LEAP jet engine fuel nozzle. Previously, it required 20 (!) separate parts and one year of time. Now, it’s a single 3D-printed unit. Additive manufacturing makes creating elements with complex geometry a child’s play, while conventional manufacturing just can’t deal with the task.
3D printing allows quickly creating non-standard parts or implementing custom designs that would otherwise be too expensive to manufacture. What’s more important, there are already industry-specific printers that can print, for instance, a denture or dental aligner in two hours (compared to 12 hours of manual work).
Advanced 3D Printing Software
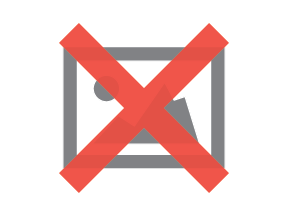
With the mass adoption of additive manufacturing, the demand for next-generation software is rising. IDTechEx reports that the global market for 3D printing software is going to grow at a CAGR of 22% by the year 2028 and will be worth $966 million.
Carbon, a 3D hardware company, has recently introduced its advanced cloud-based solution that’s backed up by the finite element analysis. It offers improved auto support, fence support, fast simulation and fleet management for scalable manufacturing.
Meanwhile, Sanvol, a startup connected with AM data, has announced its cooperation with the U.S. Navy on developing AM machine learning software. The Office of Naval Research aims at analyzing the interconnection between process parameters and material performance to reduce reliance on traditional material characterization and testing.
Here’s another interesting detail: Vishal Singh, co-founder of Link3d, believes that the additive manufacturing industry will be adopting the blockchain technology in 2018 since it offers immutability of digital files.
Conclusion
For years now the media have been hyping around the 3D printing technologies. And while in the early 2010s the hype was mostly unjustified, today the landscape has changed drastically. 3D printing, massively adopted in engineering processes, is expected to improve the work processes in many industries, creating new leaders and setting higher standards for customized and complex products. Finally, it seems like at last 3D printing is becoming all it’s cracked up to be. Don’t miss the 3D printing train!
READ ALSO
Write your own
success story
with Pwrteams!
Share your details in the form, tell us about your needs, and we'll get back with the next steps.
- Build a stable team with a 95.7% retention rate.
- Boost project agility and scalability with quality intact.
- Forget lock-ins, exit fees, or volume commitments.